Your cart is currently empty!
Understanding ATEX Certified Flow Meters: Broil Sensotek Industries
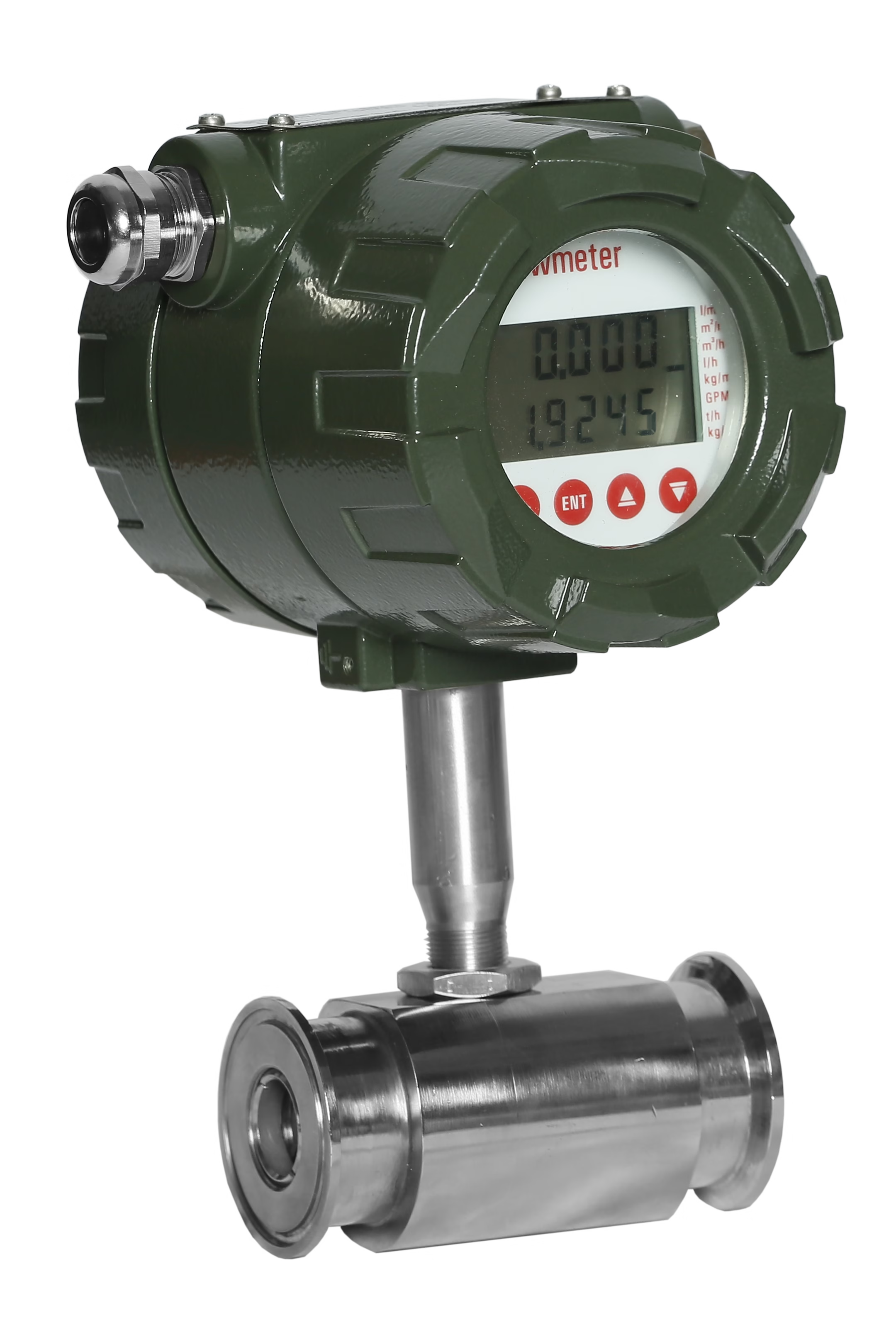
Introduction to ATEX Certification in Flow Meters
Flow meter ATEX certification refers to the compliance of flameproof equipment and protective systems intended for use in potentially explosive and atmospheres. It stands for “ATmosphères EXplosibles.” This certification is crucial within industries that handle flammable gases, vapors, or combustible dust. It directly contributes to ensuring safety and operational integrity. ATEX-certified Flow meters play a vital role in hazardous and intrinsically safe environments.
At the core of ATEX standards are two directives. The ATEX 2014/34/EU governs the equipment used in explosive atmospheres. The ATEX 1999/92/EC focuses on improving the safety and health of workers potentially at risk from explosive atmospheres. When discussing flow meters, specific designations such as ‘EX ia’ and ‘EX d’ are essential. ‘EX ia’ denotes intrinsically safe equipment. This indicates that the device will not produce any sparks or heat capable of igniting surrounding gases or dust under normal and fault conditions. Conversely, ‘EX d’ refers to flameproof enclosures. These protect sensitive components from explosions occurring inside the enclosure, thereby preventing the ignition of the external atmosphere.
The significance of utilizing ATEX-certified flow meters cannot be overstated. Employing non-compliant devices in hazardous environments can lead to catastrophic consequences such as explosions, loss of life, and extensive damage to facilities. Consequently, industries including oil and gas, chemicals, and food processing prioritize ATEX certification. This ensures that their equipment adheres to the highest safety standards. The increased emphasis on compliance not only serves to protect personnel and assets but also enhances operational reliability and efficiency. Ultimately, this leads to a more sustainable industrial practice.
Overview of Broil Sensotek Industries’ ATEX Certified Flow Meters
Broil Sensotek Industries offers a diversified range of ATEX certified flow meters. Designed to ensure safety and accuracy in hazardous environments. Among the prominent types of flow meters available are oval gear positive displacement flow meters. These are ideal for measuring viscous fluids. They operate on the principle of positive displacement, making them suitable for applications such as food processing and chemical manufacturing. In these industries, precise control over fluid distribution is essential.
Another key offering is the vortex flow meter. It is capable of measuring air, gas, and steam. This type of flow meter utilizes vortex shedding principles. This allows for accurate measurements in various industrial sectors, including HVAC systems and power plants. Its durability and minimal maintenance requirements make it a popular choice among engineers.
Furthermore, Broil Sensotek’s turbine flow meters provide high accuracy for low-viscosity liquids. The turbine’s rotation within the fluid flow generates a proportional frequency signal that reflects the flow rate. This type of flow meter, used in oil and gas applications, pharmaceuticals, and water management systems, where precision is critical.
Helical rotor velocity flow meters are another innovative option, used primarily for measuring non-Newtonian fluids. Their design enables them to handle a broad viscosity range. This is particularly beneficial in industries dealing with complex fluid characteristics, such as cosmetics and food production.
Lastly, Coriolis mass flow meters stand out for their ability to provide direct mass flow measurements. This is irrespective of fluid density or viscosity. This feature is particularly advantageous in chemical processing and biotechnology sectors. In these sectors accuracy and reliability are paramount. Overall, Broil Sensotek Industries’ range of ATEX certified flow meters exemplifies their commitment to safety, efficiency, and innovation in fluid measurement technology.
EX ia vs. EX d: Understanding the Designations
In industries where explosive atmospheres are a concern, understanding the designations of safety equipment is crucial. Two primary designations used are ‘EX ia’ and ‘EX d’. Each represents specific safety features vital for operation in hazardous environments.
‘EX ia’ intrinsically safe equipment
The ‘EX ia’ designation refers to intrinsically safe equipment. This equipment is designed to be safe under normal operating conditions, even in the presence of explosive gases or combustible dust. This type of equipment is applicable in Zones 0, 1, and 2 for gases, and Zones 20, 21, and 22 for dusts. In these zones, the equipment must not create any sparks or exceed permissible energy levels that could ignite a potentially explosive atmosphere.
Intrinsically safe devices work by limiting the energy that can be discharged, effectively making them incapable of causing ignition. The use of ‘EX ia’ equipment is particularly beneficial in environments where flammable substances are present continuously or intermittently. Their design promotes the safe operation of sensors, controllers, and monitoring equipment among other applications, ensuring compliance with ATEX regulations.
‘EX d’ : flameproof or explosion-proof equipment
Conversely, the ‘EX d’ designation indicates flameproof or explosion-proof equipment. It is designed to contain any explosion within the equipment housing. The flameproof enclosure is robust. It prevents flames from escaping and igniting the outside atmosphere. ‘EX d’ equipment is suitable for areas with higher risks, especially in Zone 1 or Zone 2 environments. In these areas, explosive gas mixtures can occur frequently. The flameproof characteristic ensures that even in the event of an internal explosion, the integrity of the device and the surrounding environment is maintained. Thus, reducing the risk of disasters.
Overall, the differentiation between ‘EX ia’ and ‘EX d’ designations signifies the need for tailored safety solutions in various industrial settings. Understanding these classifications enables industries to select the appropriate flow meters and related equipment. These should meet their safety requirements and operational demands.
Applications and Advancements in Flow Meter Technology
The industrial application of ATEX certified flow meters, particularly those developed by Broil Sensotek Industries, spans a diverse array of sectors. These include oil and gas, chemical processing, pharmaceuticals, and food and beverage. These flow meters are designed to operate within potentially explosive atmospheres. They ensure safety compliance while delivering high measurement accuracy. In environments where flammable gases or vapors may be present, the use of ATEX certified devices mitigates risks associated with ignition sources. As industries continue to emphasize safety, the demand for these specialized instruments has significantly increased.
Advancements in flow meter technology have significantly enhanced the capabilities and performance of these devices. Innovations such as magnetic flow metering, thermal mass flow measurement, and Coriolis flow measurement have resulted in more reliable data. They allow for precise control of processes. Enhanced algorithms and improved sensor designs contribute to increased accuracy and responsiveness in measuring fluid flow rates, even under varying conditions. These technological upgrades not only optimize operational efficiency but also help in achieving compliance with stringent environmental standards.
Furthermore, the integration of smart technologies and digital interfaces has revolutionized flow measurement. The adoption of IoT (Internet of Things) capabilities allows for real-time monitoring, advanced analytics, and predictive maintenance, enhancing equipment longevity. This transition towards smart flow meters is pivotal as industries continuously seek to reduce downtime and improve overall operational safety.
As we look towards the future, ongoing safety regulations and a concerted effort to enhance measurement techniques are expected to drive further innovations in flow meter design. The need for precision will likely motivate research and development. This will aim at producing more resilient and adaptable instruments for hazardous areas. Broil Sensotek Industries remains at the forefront of these advancements. They are committed to delivering cutting-edge solutions that prioritize both accuracy and safety in fluid measurement.
Leave a Reply